Industrial Automation Applications
Photoelectric sensors have revolutionized manufacturing and production processes, providing accuracy, speed, and safety enhancements across diverse industries. Here’s a closer look at their vital role:
Packaging
Fill Line Verification: Ensuring bottles, boxes, or other containers are filled correctly prevents underfilled products and costly overfilling. Photoelectric sensors excel at this task.
Label Detection: Photoelectric sensors with high-contrast or color mark detection capabilities ensure labels are present and properly aligned, streamlining the packaging process.
Seal and Cap Inspection: Verifying that caps and seals are securely in place is essential for product safety. Diffuse reflective photoelectric sensors can reliably detect the presence or absence of these elements.
Pepperl+Fuchs Expertise: Pepperl+Fuchs offers specialized clear object detection sensors (like the R10x series) optimized for transparent film and bottle detection tasks.
Conveyor Systems
Object Counting: Photoelectric sensors positioned above conveyors accurately count parts or products, supporting inventory management and throughput analysis.
Sorting and Routing: By distinguishing between materials, sizes, or colors, photoelectric sensors are key to automated sorting systems that divert items based on defined criteria.
Jam Detection: Sensors monitor for potential blockages on conveyor belts that can cause downtime, facilitating early intervention.
Bottling & Labeling
Precise Label Placement: Photoelectric sensors with small, focused light spots and color detection capabilities optimize label placement for a consistent and professional appearance.
Liquid Level Sensing in Bottles: Specialized photoelectric sensors can detect liquid levels even through colored or opaque containers, ensuring proper fill levels and preventing overflows.
Robotics
Part Detection for Pick-and-Place:Photoelectric sensors equip robots with the ability to “see” objects, enabling accurate gripping and placement operations in assembly tasks.
Collision Avoidance: Retroreflective or through-beam sensors help industrial robots safely navigate their workspace by detecting obstacles.
Assembly Line Monitoring
Part Verification: Sensors ensure the correct components are present at each assembly station, reducing defects and ensuring product quality.
Position Detection: From precise alignment of components to verifying proper ejection after a process, photoelectric sensors provide critical feedback to assembly line controllers.
When harsh environments (washdowns, heavy dust) are a concern, Pepperl+Fuchs sensors with robust housings (IP69K rated) and longer sensing distances offer a durable solution.
Logistics and Transportation
Photoelectric sensors drive efficient logistical operations, ensuring goods and materials move through the supply chain quickly and accurately. Let’s delve into specific use cases:
Warehouse Sorting
Photoelectric sensors are at the heart of automated sorting systems in vast warehouses where thousands of items need rapid organization. They detect package sizes, shapes, and even barcodes or labels, allowing for categorization and routing to the correct destinations. For challenging applications involving dark or reflective surfaces, Pepperl+Fuchs offers sensors with reliable background suppression and enhanced reflectivity compensation to ensure accurate reads.
Shipping and Receiving
Photoelectric sensors streamline loading and unloading processes. On dock doors, sensors verify that trucks are properly positioned before loading or unloading begins, enhancing safety and efficiency. Within trailers or containers, photoelectric sensors aid in package counting and ensure spaces are fully utilized while preventing overloads.
Baggage Handling
The complex conveyor networks in airports rely heavily on photoelectric sensors to guide luggage to the proper destinations. From detecting baggage as it’s placed on conveyors to sorting it based on tags or size, sensors ensure a smooth and timely flow of luggage throughout the system. In this fast-paced environment, sensors with faster response times are crucial, and Pepperl+Fuchs offers a range of sensors to suit specific performance requirements.
Safety Systems
Photoelectric sensors are a cornerstone of modern safety systems, safeguarding individuals and preventing damage to equipment in both industrial and everyday settings. Their non-contact sensing capabilities make them uniquely adaptable to diverse safety-critical applications. Let’s dive deeper into some specific examples:
Automatic Doors
Photoelectric sensors in automatic doors extend beyond simple presence detection for opening and closing. Their integration with door control systems can offer more sophisticated safety features.
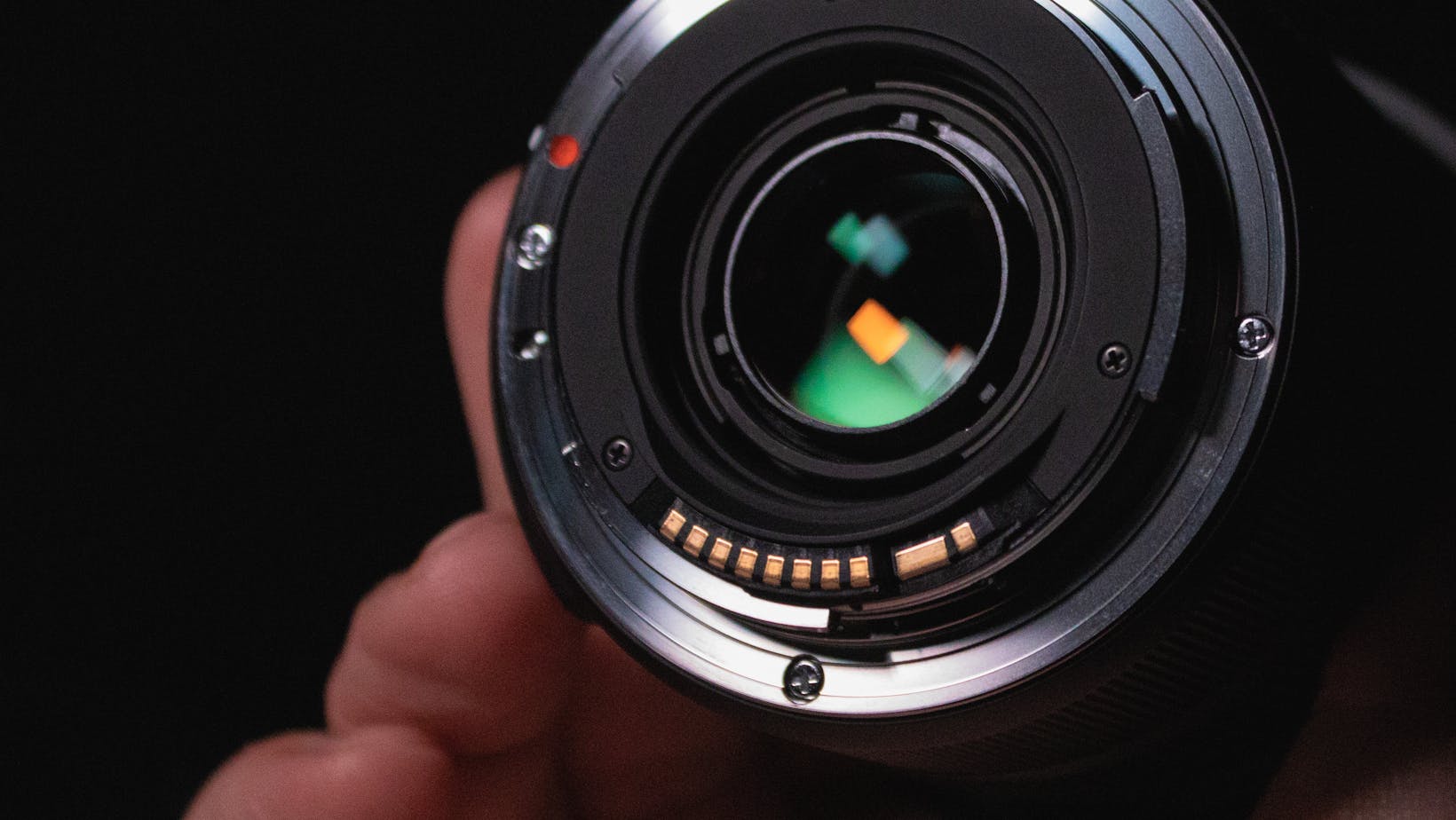
For instance, sensors positioned at varying heights can detect the direction of travel, preventing the doors from closing if someone reverses direction halfway through the doorway. Sensors with specialized filtering or background suppression capabilities should be considered to combat harsh weather or direct sunlight that can sometimes interfere with sensor operation.
Elevators
In addition to the light curtain safety function mentioned earlier, photoelectric sensors can serve other purposes within elevators. Sensors mounted near the floor can detect the presence of small objects or obstructions that may prevent doors from closing fully, alerting users or triggering an automatic reopening sequence. Within the elevator car, sensors can sometimes be used for touchless button activation, improving hygiene, or monitoring passengers’ weight distribution to signal when capacity has been reached.
Machinery Guarding
Industrial robots, presses, cutting machines, and other automated equipment require robust safety measures, and photoelectric sensors are at the forefront. Beyond the straightforward beam-break stop function, sensors can be configured in sophisticated ways for advanced protection:
● Perimeter Guarding: Multiple photoelectric sensors around a hazardous zone create a virtual barrier. Any intrusion triggers an immediate machine shutdown.
● Access Monitoring: Sensors can detect the opening of safety doors or access panels, preventing machine operation while maintenance is in progress.
● Hand Detection: Specialized photoelectric grids are used for safeguarding areas where operators must interact with the machine yet still require protection. These sensors distinguish between larger objects (arms or bodies) and permissible material fed into the machine.
Critical Factors:
● Sensor Selection: Safety applications demand sensors and light curtains that conform to rigorous standards (SIL/PL ratings). Pepperl+Fuchs offers a comprehensive range of safety-rated components and the expertise to assist with proper selection.
● System Design: The overall safety system design must factor in machine stopping distances, potential blind spots, and ensure adherence to applicable safety regulations. This often involves professional consultation or a qualified safety engineer.
The evolution of photoelectric sensor technology, with its increased reliability and advanced features, continues to enhance its capabilities to ensure people and processes’ safety.
Other Applications
The capabilities of photoelectric sensors extend to diverse domains where precision and non-contact detection offer unique advantages. Here are a few key sectors:
Outdoor Detection
Traffic Monitoring: Specialized long-range photoelectric sensors assist in traffic flow analysis, detecting vehicles and triggering signals at intersections. Sensors with weatherproof housings and resistance to environmental interferences are crucial for these applications.
Perimeter Security: Wide-area photoelectric ‘fences’ can be used to protect property or outdoor perimeters. Specialized beam patterns and advanced signal processing can minimize false alarms caused by wildlife or other disturbances.
Environmental Sensing: Research and ecological monitoring sometimes rely on photoelectric sensors to detect water turbidity levels or to trigger air quality measurements when pollution thresholds are reached.
Liquid Level Sensing
While traditional float switches are common, photoelectric sensors offer advantages in certain situations:
● Non-contact Measurement: This minimizes the risk of sensor fouling or material buildup, making them particularly suitable for viscous or sticky liquids.
● Point Level Detection: Photoelectric sensors can detect the presence or absence of liquid at a precise point in a container, enabling overfill protection or ‘pump dry’ detection.
● Challenging Liquids: Foamy liquids, or those with varying colors, can be tricky for standard sensors. Specialized photoelectric sensors with more focused light beams or adaptive settings can overcome these issues.
Medical/Pharmaceutical
Hygiene, accuracy, and reliability are paramount in these sectors, making photoelectric sensors a natural fit for:
● Counting Pills or Small Medical Parts: High-speed precision counting on conveyor systems relies on sensors with excellent repeat accuracy and fast reaction times.
● Label Verification: Ensuring proper medication labeling or the presence of barcodes is vital. Photoelectric sensors with color detection or high contrast capabilities excel at this.
● Liquid Sensing in IV Bags: Specialized sensors can detect the liquid-air interface in IV bags, signaling when a bag is running low or alerting to potential air bubbles in the line.
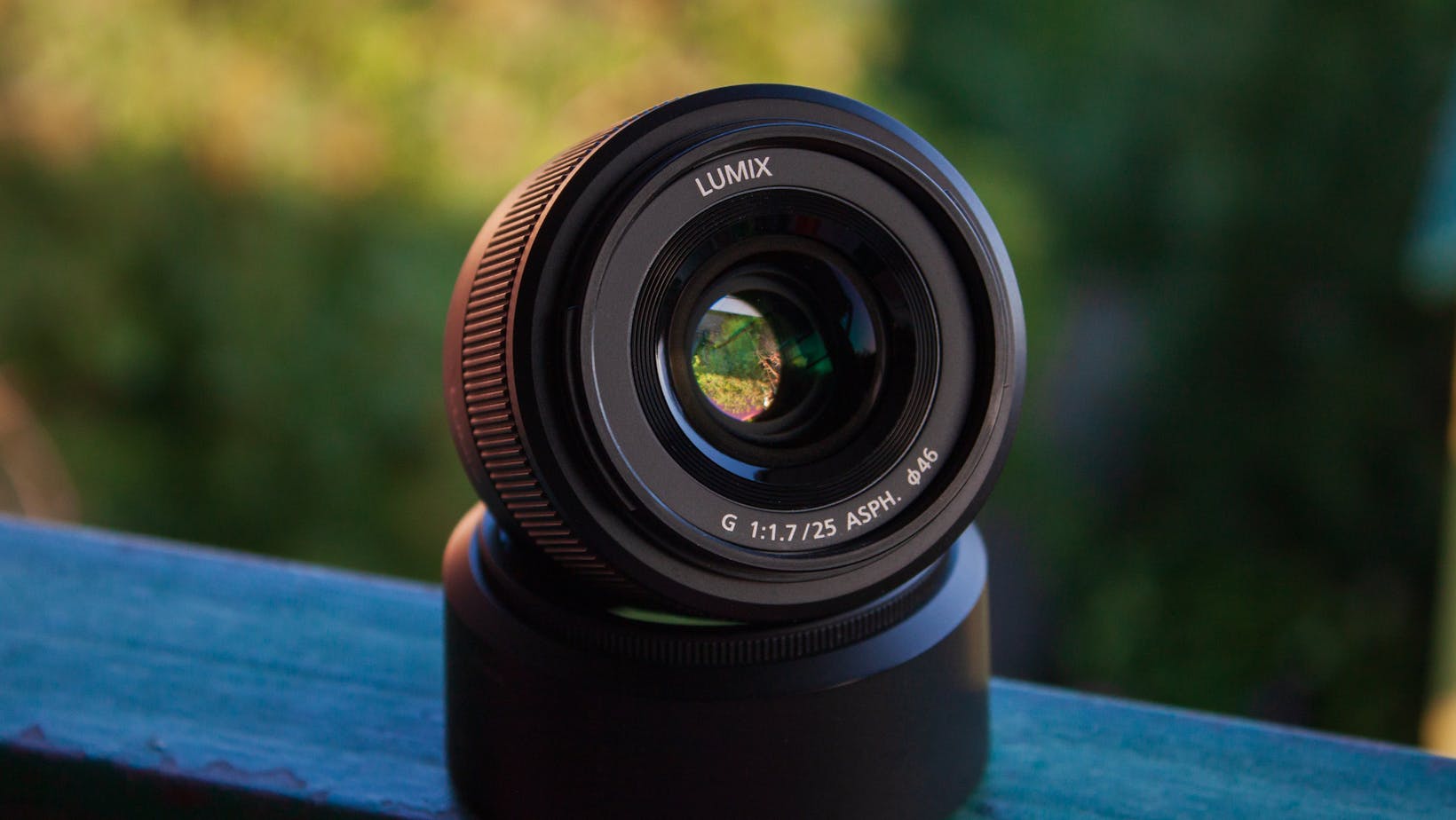
Harsh washdowns, chemical compatibility, and strict regulatory requirements often necessitate specialized sensors in medical and pharmaceutical settings. Pepperl+Fuchs offers sensors with hygienic stainless-steel housings and certification for these demanding environments.
The versatility of photoelectric sensors is truly remarkable. From the precision of factory floors to the vastness of logistics networks, their ability to reliably detect objects and materials has transformed numerous industries. As their technology advances, we can anticipate photoelectric sensors finding even more innovative applications.
Key Takeaways:
● Photoelectric sensors are essential for automation, streamlining production, and enhancing efficiency.
● Safety systems rely heavily on photoelectric sensors to protect workers and prevent accidents in industrial environments.
● Their adaptability extends beyond traditional manufacturing, with growing uses in transportation, environmental monitoring, and even the healthcare sector.
The future for photoelectric sensors is bright. As sensor capabilities increase and their integration with smart systems expands, they will continue to play a pivotal role in shaping how we manufacture, transport, and interact with the world around us.